EPS Pre-Expander XPand 860 - All in One Pre-Expander - CE & FCC.
15000 EUR - Ready to Work
Built in STEAM GENERATOR (no need to buy one).
NO need of COMPRESSED AIR.
NO need of STEAM ACCUMULATOR.
Product Overview :
The Pre-expander plant "XPand 860" produce by VirtuaVia Ltd is intended to expand polystyrene beads and has embedded STEAM GENERATOR of low power (15 kW), unlike steam generators offered on the market (those power is 50-150 kW).
The polystyrene granules are expanded in the Pre-Expander "XPand 860" by the method of heat processing with saturated steam.
The Pre-Expander "XPand 860" is compact and can be placed directly on production sites. The production and use of the unit does not require complex operations and optional technological equipment.
Just connect the "XPand 860" with mains supply (380V) and water pipeline.
The possibility to place this Pre-Expander directly where you need it on construction/production sites of polystyrene beads or concrete preparation allows to cut charges on transportation.<br>
The drying unit is intended for the technological drying of foamed granules. During the expansion the EPS granules contain up to 10-15% of moisture, and just before the forming stage the foamed material should contain only minimum residue of moisture, sufficient to make cells active, that make easier the filling of molding plant. In the a drying plant the process of granules drying is accelerated due to evacuating of access moisture by air heat treatment.
It leads to that the inner pressure stabilizes and the external walls of granules are strengthen. The air heated up to 35-40°C is supplied continuously into the drying unit.
The penetration of air into the cells of the expanded polystyrene (EPS) gives to the material the high parameters of compressive strength.
The Pre-expander "XPand 860" unites have all necessary units and devices into one frame. It considerably simplifies the transportation, installation, operation and maintenance of the unit.
The general frame represents a welded construction made from a shaped tube and a sheet metal plate on which the chamber of the thermal treatment and the drive of the raw material feeder screw are installed.
The thermal treatment chamber is cylindrical and is made from sheet steel.
In the upper part of the chamber the gear motor of the agitator drive is installed. On end covers of the chamber the cases of bearings is installed.
The agitator's shaft is based on them. On the shaft the agitator's blades of expanded EPS granules are installed. In the lower part of the chamber end cover there is a steam expander connected with steam pipeline,
and also a pipeline of condensate removal. The screw of raw material supply connected with drive electric motor installed on the general frame is cut in.
The chamber has a door on half of altitude of the chamber that makes easy the access to all parts of agitator and the shaft.
Devices and the assembly units applied in the Pre-Expander "XPand 860", allows to mechanize as much as possible the expansion of polystyrene granules.
The control unit of the water level in the steam generator and temperature the relay load cell of heating elements allow to adjust the complex once for the set expansion mode.
Feeder's screw ensures the uniform feed of raw materials in the thermal treatment chamber. The agitator's device, installed inside of the chamber, prevents the sticking of expanded granules.
The EPS expansion unit "XPand 860" is equipped with optional screw feeder of pre-expanded polystyrene granules supply for repeated processing with saturated water steam.
Advantages of the XPand 860:
- Built-in STEAM GENERATOR.
- NO need of air compressor.
- NO need of Steam Generator (already inside).
- NO Steam Accumulator needed.
- Compact construction.
- High capacity.
- Low power consumption.
- Competitive price at high quality of components.
- System of adjustment and control of steam temperature SUPER STEAM.
- Application of qualitative gear motor as a agitator's drive.
- Application of terminal regulator of OVEN production.
Technical characteristics :
Power consumption, kW : 9.00
Dimensions : 1000 × 2000 × 2500 mm
Weight : 400 Kg
Primary Expansion : 15-30 g/l
Secondary Expansion : 8-15 g/l
Noise Level : 60 Db
Voltage : 380
Expansion chamber volume : 860 liters
Volume of raw material hopper : 40 liters
Capacity, m³/shift : 80
Density 15 g/l : 10 m³/h or 150 Kg/h
Density 30 g/l : 18 m³/h or 540 Kg/h
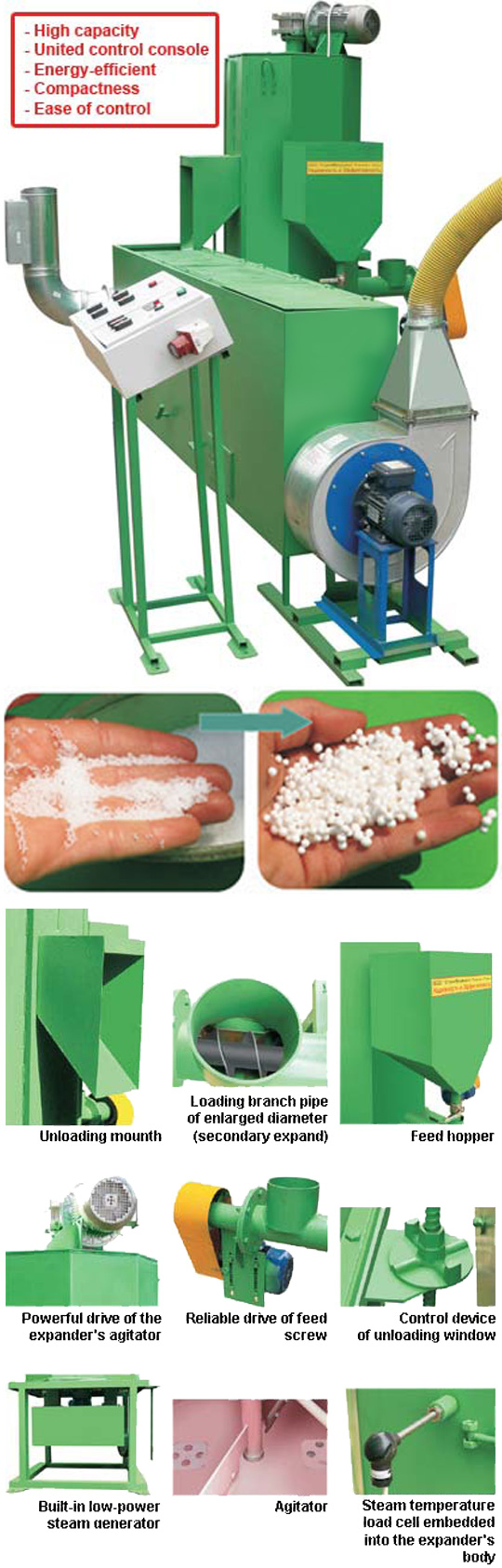